
- FSAE TIRE COEFFICIENT OF FRICTION DRIVER
- FSAE TIRE COEFFICIENT OF FRICTION SOFTWARE
- FSAE TIRE COEFFICIENT OF FRICTION FREE
The Pneumatic Tire National Highway Traffic Safety Administration Washington, DC 2006Įvans, Larry R. Suspension Geometry and Computation Chichester, UK John Wiley & Sons Ltd 2009 978-1-6 Mass Properties and Advanced Automotive Design SAWE Technical Paper 3602, 74th SAWE International Conference on Mass Properties Engineering Alexandria, VA 2015ĭixon, John C. Rolling Resistance of Pneumatic Tires as a Factor in Car Economy SAE Technical Paper 420080 1942 10.4271/420080 Mechanics of Vehicles Cleveland, OH Penton Publishing Company 1957īillingsley, W. Fundamentals of Vehicle Dynamics Warrendale Society of Automotive Engineers, Inc. Properties of Tires Affecting Riding, Steering and Handling SAE Technical Paper 350082 1935 10.4271/350082 La Suspension de la Direction de la Voiture Automobile: Shimmy et Danadinement”, Société des Ingénieurs Civils de France Bulletin 78 5Įvans, R. Schwingungen in Automobillenkungen Krayn, Berlin 1931īroulheit, G.
FSAE TIRE COEFFICIENT OF FRICTION DRIVER
In the joint velocity driver of the transmission a spline curve command the rotational speed starting from zero and it will be increased until the car goes into a spin.Becker, G. To understand how the antiroll bar work we have to try another simulation in which the steer wheel remains hold in the same position. Was sought the best performance increasing the speed of the car and comparing results with different tires and different layout of the antiroll bar. In this simulation the car is driven by a closed loop control that compare the position of the chassis with the track to follow.
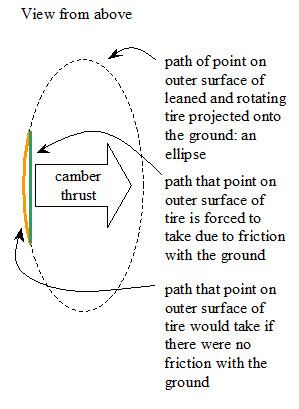
The vehicle have to ride a track which have the shape of the 8 and the teams receive score for best lap time. In the next simulations the behavior of the car will be compared in 3 cases: without any antiroll bar, with front antiroll, and with rear antiroll. Therefore the antiroll bar work only for non symmetric stress. The rotational movement of the bar is related to the rotational movement of the adjacent rocker.Ī device between the half bar is insert to provide the torsional stiffness of 100 Nmrad to the bar. In this analysis, in the complex tire model were inserted values related to tire pressure 0,8 bar and camber angle (IA) zero.
FSAE TIRE COEFFICIENT OF FRICTION SOFTWARE
This table is used by the software to build a spline surface to evaluate the Lateral Force for each couple of slip angle and normal force during the simulation. Fsae Tire Coefficient Of Friction Software To Build In this case is used the Complex Tire which need some input. The movement between rocker and chassis is related to the force calculated trought Stiffness and Damping coefficients in the TSDA.

Sensor axis system are used to control if the base of the coachwork collide with the ground in the simulations.
FSAE TIRE COEFFICIENT OF FRICTION FREE
They transmit the same rotational speed to the wheels and they let free the vertical degree of freedom of the suspension. Fsae Tire Coefficient Of Friction Free The Vertical

The axles shaft are connected from the transmission body to the hubs. The rotation speed is defined trough a spline engine that plot rpm-time. The chassis count the mass property of all the non model components like engine, cooling system, safety devices, and driver too, for a total mass of 256 kg.Ī device with Stiffness-Damper property is then used to simulate the spring damper force between rocker and chassis.
